(1) Automatic filter press
The conventional filter press is manual, manual discharge, intermittent production, long filtration cycle, low productivity, heavy equipment, and labor intensity. With the development of modern industry, new automatic filter presses have been introduced. The structure of the filter press has been improved and new materials and program control systems have been used. Widely used in chemical, metallurgy, building materials, petroleum, coal, pharmaceutical, ceramic industry and environmental protection sectors. Especially in mines with high grounds, filter presses are almost the only equipment that can be used when vacuum filtration is difficult to achieve the expected pressure difference.
The automatic filter press uses intermittent pressurization to pass the liquid through the filter cloth to achieve solid-liquid separation. The utility model has the advantages of continuous operation, high filtration pressure, low moisture content of the filter cake, simple structure, stable operation, long working life of the machine and easy maintenance. The filter cake has the function of a filter layer, the solid phase recovery rate is high, and the filtrate is relatively clear. Less power consumption. The disadvantage is that the strength and manufacturing precision of the components are required to be high, the cost is high, the intermittent feeding, and the unit filtration area yield is not high.
The design of the filter press is limited to increasing the pressure difference and the filtration area, appropriately extending the filtration time, and also using the fine pore filter cloth and increasing the thickness of the filter cake, so that the filtration efficiency is also high when processing the fine and sticky slurry.
Tests have shown that the use of a filter press to treat dilute fine-grain viscous materials has significant advantages. For example, when the filter press electrolytic manganese leaching solution, to improve its processing than ordinary filter 4 to 5 times, reducing cake moisture, improving the washing effect, thereby improving the recovery rate, the other filter to solve the problem can not be solved. When processing the flotation of nickel sulfide concentrate, the filter cake moisture can be stabilized at about 16%. Compared with the external filter, the filter cake moisture can be reduced by 7% when the unit filtration area yield is slightly higher. Thereby greatly reducing the drying cost. For -0.043 mm (325 mesh) of 97% of the rare earth concentrate, in the case of a ore concentration of 8-12%, with a concentration of 10% of the re-concentrated concentrate into the filter press, filter cake moisture It can be reduced to 8 to 10%, which is 6 to 8% lower than the filter cake moisture of the drum filter, so that the concentration and drying operations can be eliminated.
The filtration speed of the filter press increases with the increase of the feed pressure. The foreign filter press uses a high-pressure plunger pump or a diaphragm pump to feed the pressure at 981 to 2453 kPa (10 to 25 kg/cm 2 ). In China, sand pumps and air compressors are often used for feeding, and the pressure is low.
Soviet Union by filtration area of the filter press type ΦⅡAKM m 2 plant tests were made on the magnetic iron ore.
The Soviet Brucevik Mining Company used the multi-layer vertical automatic filter press from the Larox company in Finland to expand semi-industrial tests on molybdenum , lead and zinc concentrates. The results showed that, for this fine sulfide, the filter cake moisture can quickly be reduced to 6 to 8.5%. This automatic filter press has been used (in the country about Finland, North America, Canada and some other beneficiation plant 1600 units), all of which saved the drying operation. The United States and Japan have developed the Lasta horizontal automatic filter press. Butte (Butte) concentrator for concentration of 65% copper concentrate dewatering, compared with ordinary dehydration, the production cost is reduced from 40 to 60%, 30 to 50% decrease in investment. The filter cake was water 8 to 10%, the original filtration and drying operations were cancelled.
At present, automatic filter presses at home and abroad are developing rapidly, with many types and specifications. The largest filter area has reached 1,250 m2 . Among them, the Larox filter press and the van automatic filter press play an important role.
A Larox automatic filter press The Finnish 34567 filter press uses diaphragm press filtration. The machine combines the advantages of a filter press, a drum filter and a belt filter. The filtration rate is large, the moisture content of the filter cake is low, and the yield per unit area is high. However, equipment costs are high. The 34567 automatic filter press is available in both vertical and horizontal versions. [next]
a Larox-PF filter press
It is a vertical automatic filter press, and its structure is shown in Figure 1. The filter plate of the vertical automatic filter press is placed horizontally, and the pair of sub-assemblies are stacked up, and the whole machine is vertical. According to different specifications, the number of filter plates is 6-20 respectively. Figure 2 is a schematic diagram of the pressure filtration process of the device. Each of the filter plate components is composed of an upper and a lower plate, a frame, a rubber diaphragm, a filter chamber, a filter cloth, a grid guide roller and a scraper. The filter frame consists of a movable bottom plate and a fixed top plate. The filter cake is pressed between the two plates and the filter frame is tightened in the groove of the base. The filter cloth is an endless belt woven from polypropylene fibers, which are alternately twisted back between the filter sheets. The filter cloth starts from the driving wheel, and is wound around the filter cloth to enter the flushing water collecting tank. The washing cloth is washed by the flushing nozzle, and then returned to the filter cloth driving roller. The tightness of the filter cloth can be adjusted by the tension roller. The slurry enters the filter chamber through the distribution pipe. The filtrate is discharged from the filter chamber and passed through a hose into the filtrate collection tube. The whole process is divided into six steps, namely filtration, diaphragm pressurization (feeding high pressure water by pressure pump; pressing filter cake by diaphragm), washing the filter cake, pressing the diaphragm after washing, blowing compressed air to remove the cake. Residual water, draining filter cake. [next]
After blowing the filter cake, the connecting rod of the filter press moves, the top plate and the bottom of the filter chamber are pulled apart, the filter cloth drive wheel starts to work, and the filter cloth can move freely, like the belt conveyor, the filter cake is separately The left and right sides are discharged. When the filter cloth passes the end of the guide roller, the filter cake falls off the filter cloth, and the unshed cake is scraped off by the blade. When the filter cloth moves up, the filter cloth flushing water system starts to work. Since the filter cloth runs alternately between the filter plates, the filter cake is not formed on the same side of the filter cloth in each cycle, the flow direction of the filtrate often changes, and the filter cloth is easily washed. The filter cloth is held in equilibrium by the adjustment roller. The time control and the recurring work of each process in the whole process of filtration are controlled by the automatic control cabinet. The length of each process depends on the nature of the filter material and other conditions.
The filter press has been widely used in many metal and non-metal ore dressing plants and chemical plants.
A nickel mine in Outokumpu, Finland, has replaced the original vacuum filter plus dryer with this equipment. The filter cake moisture decreased from 18 to 20% to 8 to 9%.
b Larox-CF and Japan and the United States jointly developed the Lasta filter press The two filter presses are horizontal automatic filter presses. The former structure mainly includes a vertical filter plate main frame, a pressing plate closure and a filter cloth rotation system. The maximum filtration area has reached 200 m 2 . The latter is also a chamber filter press, which is pressurized with compressed air.
The difference between the B-box automatic filter press and the plate-and-frame filter press is that the filter chamber of the former is alternately arranged by a concave filter plate and a press filter plate with a squeeze diaphragm, and has double-sided filtration and efficiency. High and medium feeding performance, easy replacement of filter cloth, large size, anti-corrosion of filter plate and wide application industry, it is more widely used in China than plate and frame filter press. In the early 1980s, China successfully developed the horizontal fully automatic YSM34011500 filter press. In 1086, it developed the XMZ1050/2000 automatic filter press that surpassed the world advanced level, making China the third largest in the world. The state of the automatic filter press. The machine adopts integrated hydraulic control, four-cylinder synchronous pressurization, automatic unloading cake, and automatic flushing filter cloth. The degree of automation ranks first in China and attracts attention from the international market. When XMZZ1050/2000 automatic filter press is used to treat slime, the feedstock has -120 mesh and 63%, and the feed pressure is 785-981% kPa (8-10 kg/ Cm), concentration 300-500 g / liter, filter cake water 21.3%, overflow concentration 0.03 g / liter, net filter press time 10 minutes to 38 minutes. Press-batch, each cycle took 65 minutes, the material can handle one thousand 21.3 tons, equivalent to single production capacity of 19.9 tons / (time-sets). The whole machine by the filter plate 150 composition. Its structure is shown in Figure 3. At present, three kinds of automatic filter presses with 340 m 2 , 500 m 2 , and 1050 m 2 can be set. The future plans to develop into small specifications to form a series of products.
The automatic filter press has a small filter area, a high filtration pressure, a low water content of the filter cake, a large filtration capacity, a simple structure, easy operation, and few failures. The filtrate is filtered to obtain a clear filtrate, and the water recovery rate is high. . However, the filter plate is placed vertically, which is disadvantageous for filter cake washing, and a vertical automatic filter press has appeared. The filter plate is placed horizontally, and the self-heavy cake is completely disposed, and the floor space is small. However, the vertical filter press is higher and the filter area is smaller. [next]
(2) Belt filter press The common features of the belt filter press are: simple structure, convenient operation, continuous feeding, high operating rate and low energy consumption. The filter cake water is generally lower than the vacuum filter. However, the crushed mud needs to be flocculated, and the quantitative addition of the flocculant is complicated, which affects the production cost, and the flushing filter cloth has a large amount of clean water. The filter cloth wears faster, and the concentricity adjustment of the drum and the roller is difficult. Compared with the frame and frame filter press, the belt filter press has reduced the capital investment by 50%, the production cost by 30%, and the production capacity by about double. Compared with the sedimentation centrifuge, the filter cake has low moisture content and a production capacity of 1 to 1.5 times higher.
Belt filter press typically consists of a press part and a drain part, pressing a press bar positioned between the two filter cloths slurry, pressure is generally 196 to 981 kPa (2 to 10 kg / cm 2). Such The equipment was originally developed to deal with municipal sludge, and was gradually extended to mines and other industrial fields, and developed rapidly. Currently, the most wide-band filter reached 4.2 m, 100 m 2 of filtration area. Our DY0.45 ~ 1.6 developed a belt filter press. The coal division has purchased a patent for the belt filter press from Arus-Amdrotz and has manufactured and sold it. There are many types of belt filter presses abroad, which can be divided into continuous pressurization and intermittent pressurization.
A continuous pressure belt filter
The continuous pressurized belt filter (Fig. 4) relies on both vacuum and pressure for dewatering. For sludge that is difficult to dewater, the effect is very good. The filter has an annular screen belt of synthetic fiber or metal wire, and a pressure belt of the same direction as the endless belt is pressed against the rear portion. After the slurry is added, it is first subjected to a vacuum to remove free water and pore water, and then the slurry is squeezed between the two belts, and the material is continuously dehydrated under pressure. After the material enters the wedge-shaped passage, it is subjected to increasing pressure to accelerate the dehydration speed. Then, under the action of the elastic pressure roller, the filter cake volume is further compressed to reduce the moisture content. A cleaning device is installed on the annular screen belt for cleaning the screen belt. In order to integrate transportation, filtration and extrusion, a pressure belt filter with a shearing roller system has been developed abroad (Fig. 5). This filter is filtered in advance by vacuum and filtered. The belt has a higher strength and a good shear roller system, so that it is not necessary to rely on the pressure from the outside to cause the tension of the belt to dehydrate and remove a large amount of moisture from the filter cake.
Mini Automatic Vacuum Forming Machine
Mini Automatic Vacuum Forming Machine applications
1. Plastic forming machine for packing is suitable for materials like VC,PE,PET,PC,PP,HIPS,APET,PETG,PS, etc.
2. Can be used to produce snack box, fruit tray , biscuit box ,toothbrush ,battery , gift, little hardware ,stationary, decorative article, pill,etc.
Mini automatic Vacuum Forming Machine Advantages
1. Plastic forming machine for packing switches to new energy-saving heat tiles which can save at least 20% energy.
2. Mitsubishi inverter as a master control system. Material length is accurate to within ± 3mm.
3. By adopting universal mold plate, Plastic forming machine for packing can save material 15%.
Mini automatic vacuum forming machine Features
1. Auto-running furnace design instead pushing by hand, It really saves manpower meanwhile improves working efficiency and forming products quality.
2. Button control or foot pedal control
available, convenient operation.
3. 25pcs ceramic infrared heating boards which
can be controlled separately, suit for different size or different thickness
material.
4. 25pcs Solid state voltage regulators, control
heating boards simple and visualized.
5. Large-scale cooling fan which can cool the
products quickly.
6. Water-spray cooling system which suit for
thick material.(optional).
7. Manual style and Semi-auto style available.
Mini automatic vacuum forming machine parameters
Model |
HX-61 |
Power supply |
AC220V OR 380V,380V/3 |
Power |
12.5KW |
Max.forming size |
560*610*180mm |
Max. forming height |
200mm |
Capacity |
60-90times/hour |
Thickness of material |
0.2~1.5mm |
N. weight |
600KG |
Machine size |
1600*720 *1900mm |
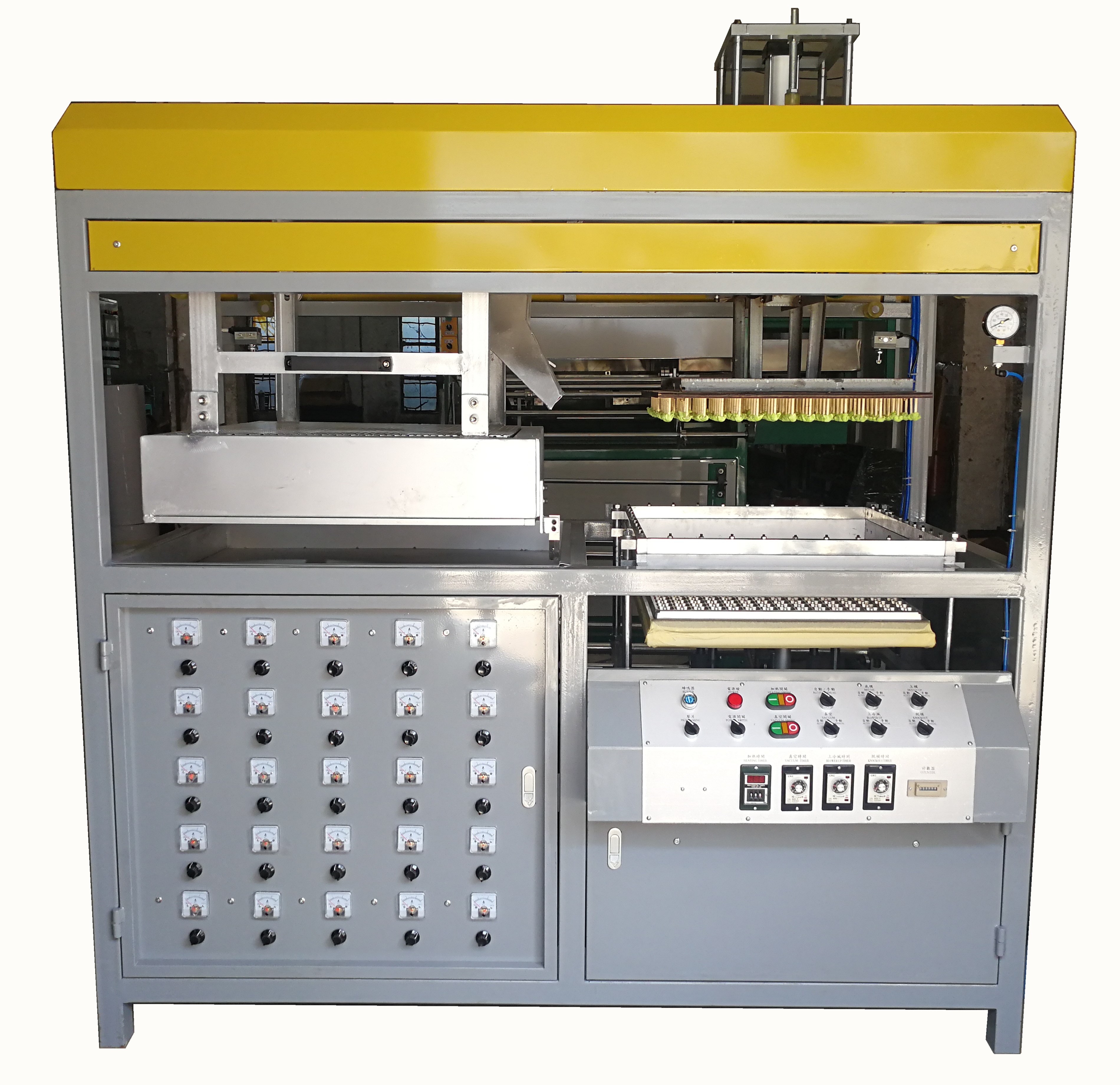
Mini Automatic Vacuum Forming Machine
Mini Automatic Vacuum Forming Machine,PVC Automatic Vacuum Forming Machine,Automatic Blister Mini Vacuum Forming Machine,Fully Mini Automatic Vacuum Forming Machine
ShenZhen Hengxing Machinery Factory , http://www.szchxjx.com