plastic pellet extruder machine plant
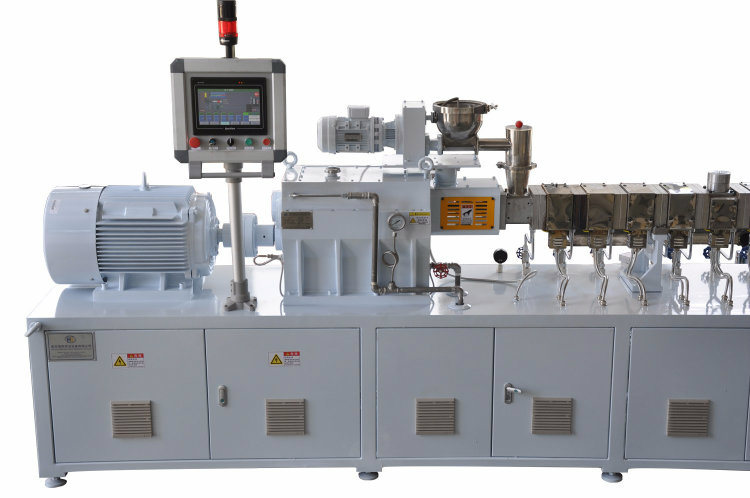
You can use our parallel twin screw extruder for:
 polymer compounding and filler masterbatch making,
 engineering polymer and glass fiber reinforcement,
 functional and color masterbatch extrusion,
 cable compounds,
 shoe sole compounds,
 powder coating materials extusion,
 degassing and devolatilization,
 direct extrusion
Â
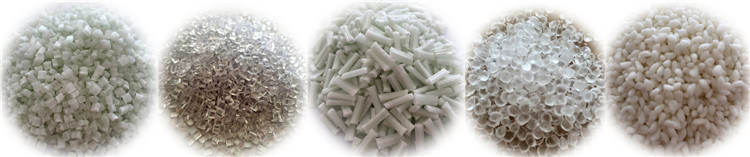
Main features: 1. Die face water ring pelletizing is suitable for most filling or not-filling hot plastic material products,Â
because it formed water ring in the outer template, templates does not touch cooling water, this feature ensures uniformity of template temperature .2. As a result of die face hotcutting system, not only insure the sleek appearance of material particles, and because the pellets were in time water cooling after cutting, so that make compact structure, reduce equipment space.
Â
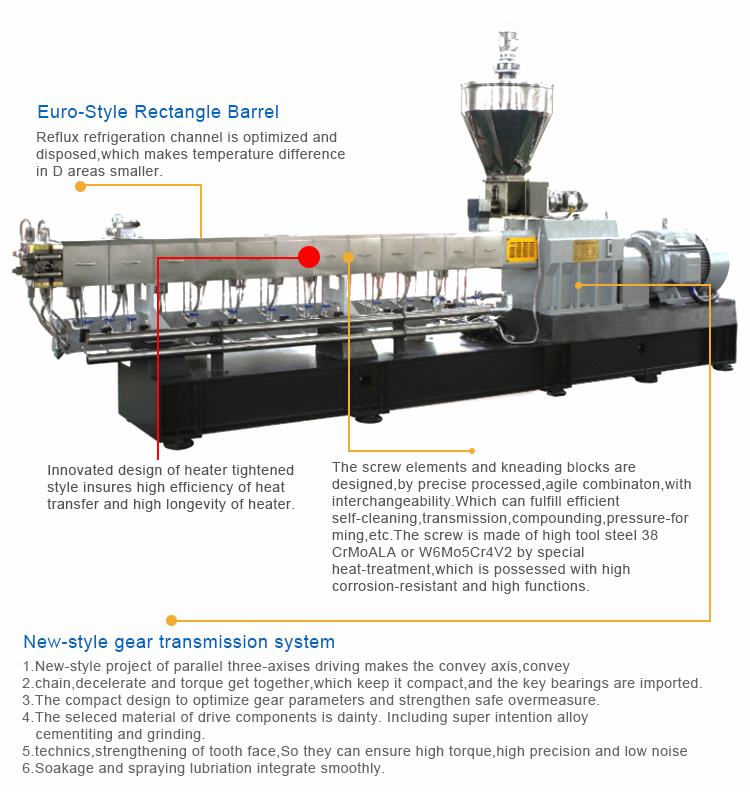
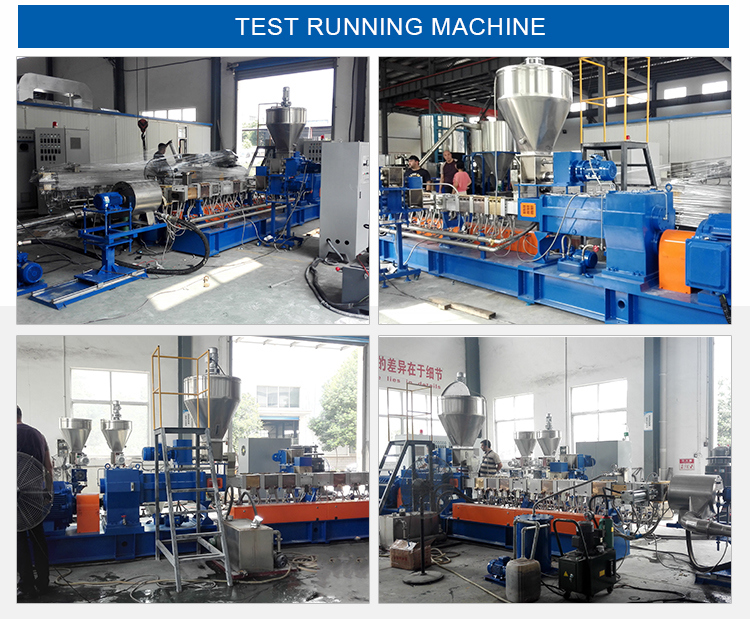
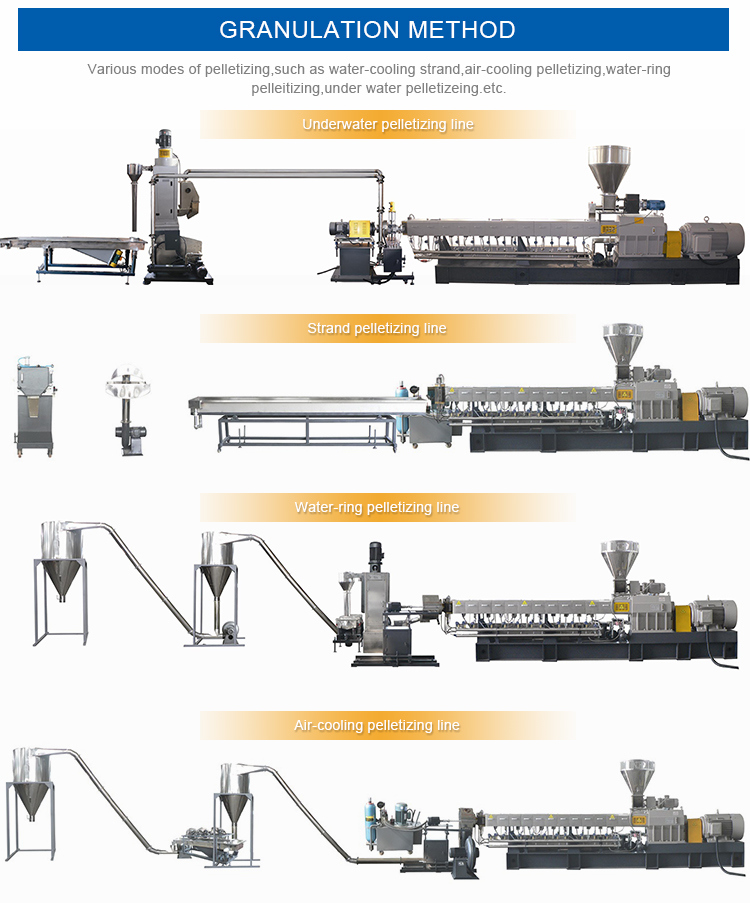
Our machine types:
1. Co-Rotating Parallel Twin Screw Pelletizing Extruders
2. Pelletizing Extruders
3. Die Face Cut (Air Cooling) Pelletizing Extruders
4. Double Stage / Double Degassing Recycling Extruders
5. Crushers, Mixers, Storage Tanks, Vibrators, Granulators, Blowers
6. Extruder spare parts
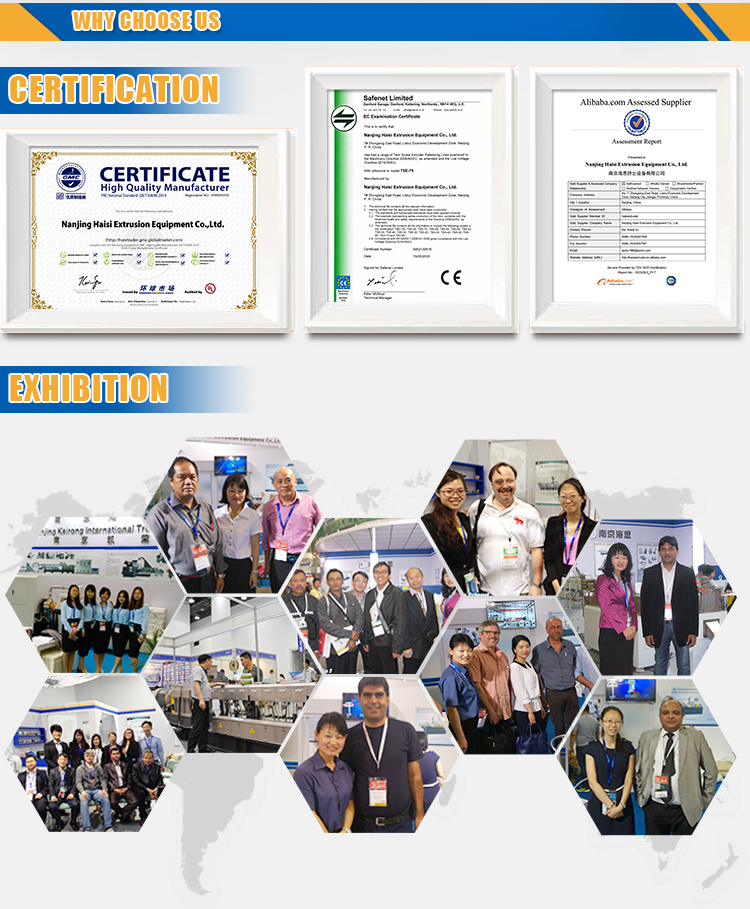
Mode | Screw Diameter D(mm) |
Screw Length(mm) | L/D | Screw Rater N(r/min) |
Motor Power P(kw) |
Torque T(N.m) |
Torque Lvel T/N3 |
Capacity Q(kg/h) |
TSE-40B | 41 | 160 | 32-52 | 600 | 30 | 239 | 5.8 | 90-150 |
TSE-52B | 51.5 | 210 | 32-64 | 600 | 55 | 438 | 5.5 | 225-250 |
TSE-65B | 62.4 | 240 | 32-64 | 600 | 90 | 716 | 5.1 | 200-300 |
TSE-75B | 71 | 290 | 32-64 | 600 | 132 | 1050 | 4.8 | 350-550 |
TSE-75D | 71 | 290 | 32-64 | 60O | 220-250 | 1990 | 9.2 | 500-1000 |
TSE-95B | 93 | 360 | 32-64 | 600 | 315 | 2506 | 5.3 | 800-1200 |
plastic pellet extruder machine plant
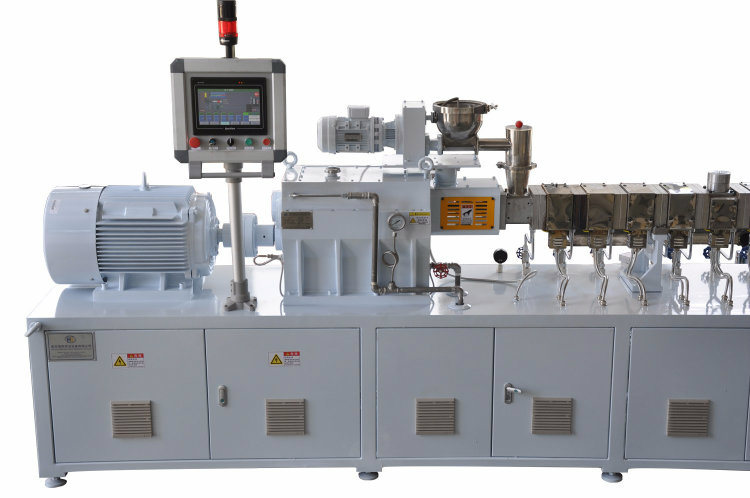
You can use our parallel twin screw extruder for:
 polymer compounding and filler masterbatch making,
 engineering polymer and glass fiber reinforcement,
 functional and color masterbatch extrusion,
 cable compounds,
 shoe sole compounds,
 powder coating materials extusion,
 degassing and devolatilization,
 direct extrusion
Â
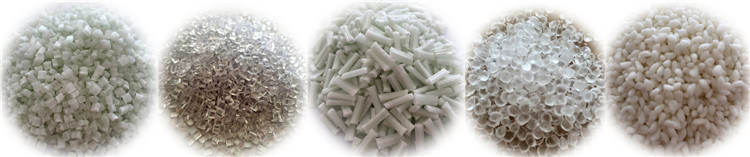
Main features: 1. Die face water ring pelletizing is suitable for most filling or not-filling hot plastic material products,Â
because it formed water ring in the outer template, templates does not touch cooling water, this feature ensures uniformity of template temperature .2. As a result of die face hotcutting system, not only insure the sleek appearance of material particles, and because the pellets were in time water cooling after cutting, so that make compact structure, reduce equipment space.
Â
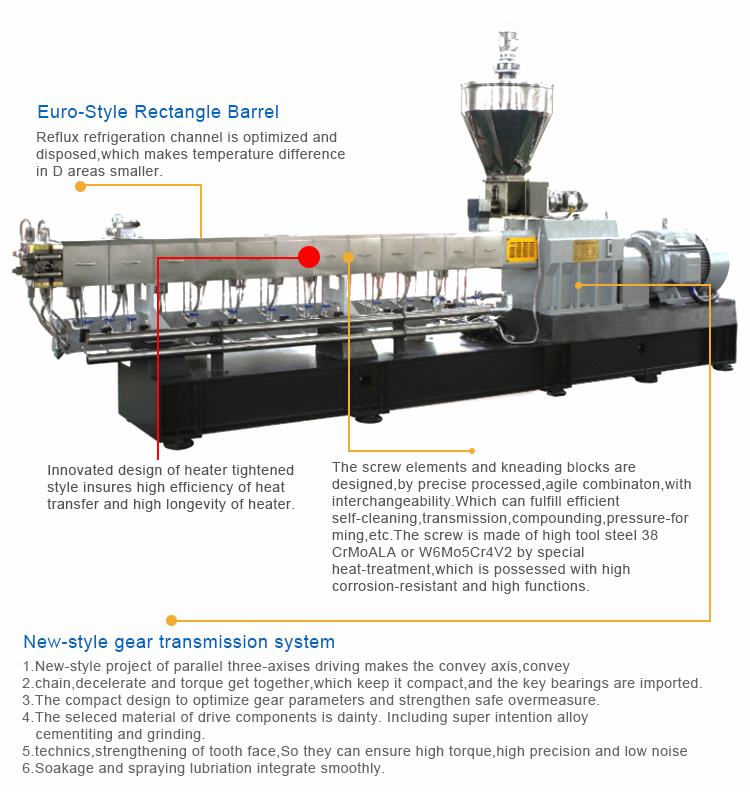
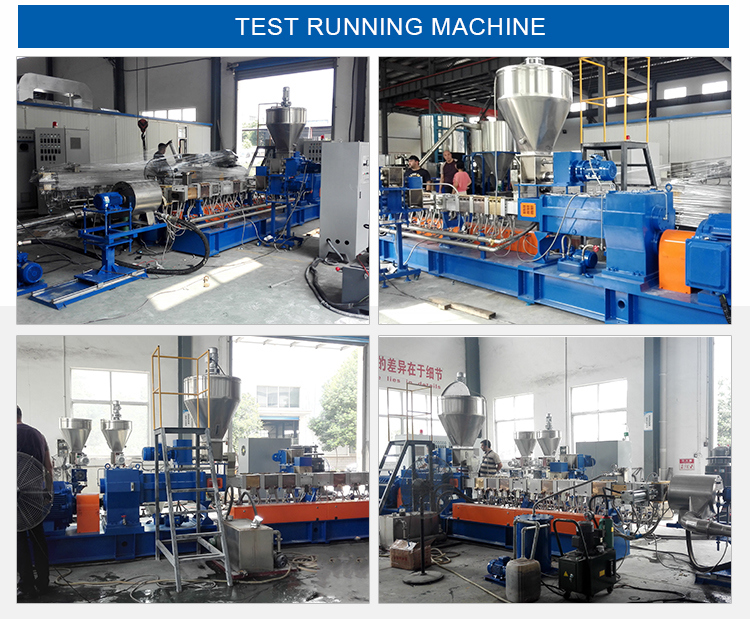
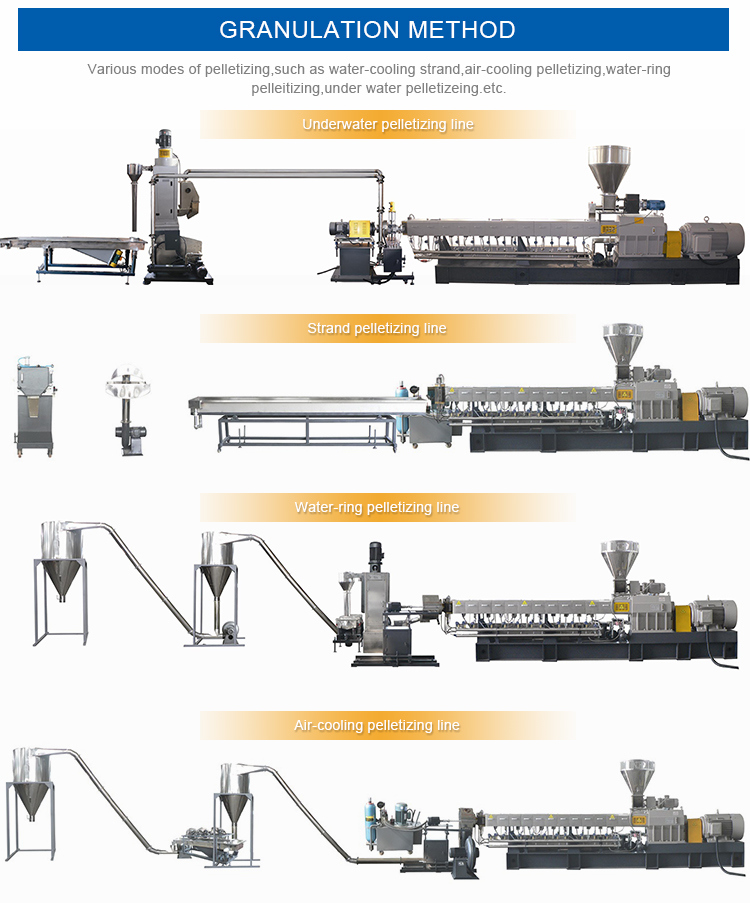
Our machine types:
1. Co-Rotating Parallel Twin Screw Pelletizing Extruders
2. Pelletizing Extruders
3. Die Face Cut (Air Cooling) Pelletizing Extruders
4. Double Stage / Double Degassing Recycling Extruders
5. Crushers, Mixers, Storage Tanks, Vibrators, Granulators, Blowers
6. Extruder spare parts
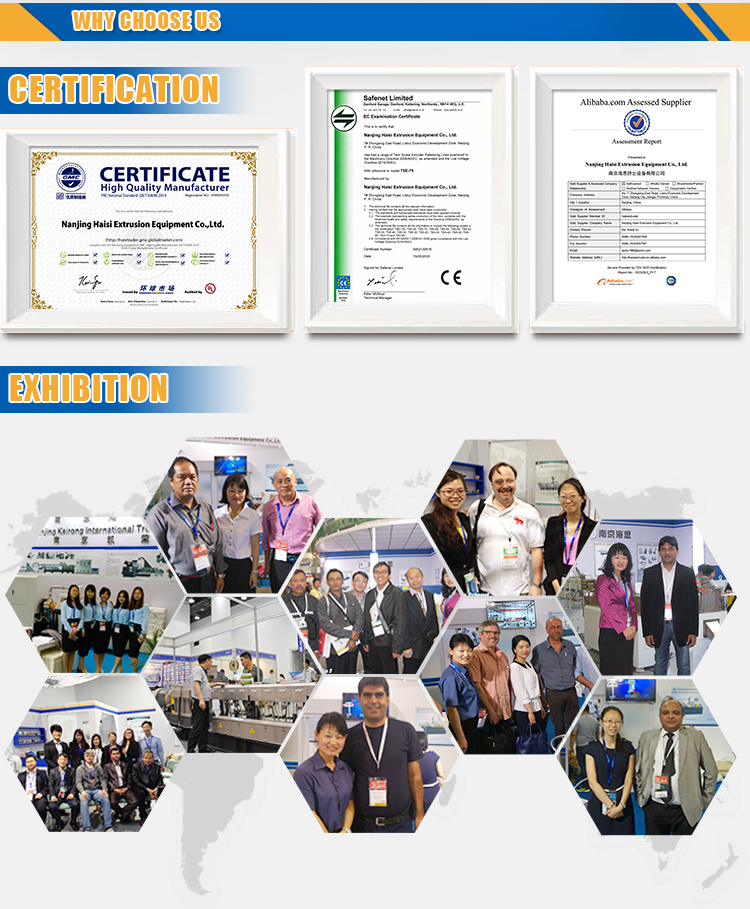
Mode | Screw Diameter D(mm) |
Screw Length(mm) | L/D | Screw Rater N(r/min) |
Motor Power P(kw) |
Torque T(N.m) |
Torque Lvel T/N3 |
Capacity Q(kg/h) |
TSE-40B | 41 | 160 | 32-52 | 600 | 30 | 239 | 5.8 | 90-150 |
TSE-52B | 51.5 | 210 | 32-64 | 600 | 55 | 438 | 5.5 | 225-250 |
TSE-65B | 62.4 | 240 | 32-64 | 600 | 90 | 716 | 5.1 | 200-300 |
TSE-75B | 71 | 290 | 32-64 | 600 | 132 | 1050 | 4.8 | 350-550 |
TSE-75D | 71 | 290 | 32-64 | 60O | 220-250 | 1990 | 9.2 | 500-1000 |
TSE-95B | 93 | 360 | 32-64 | 600 | 315 | 2506 | 5.3 | 800-1200 |
A duster
Dust remover is a device that separates dust from flue gas. It is called Dust Collector or dust removal equipment. The performance of the dust collector is expressed by the amount of gas that can be treated, the resistance loss of the gas through the dust collector and the efficiency of the dust removal. At the same time, the price of dust collector, the cost of operation and maintenance, the length of service life and the difficulty of operation management are also important factors to consider its performance. Dust catcher is a common facility in boilers and industrial production.
A brief introduction of dust remover
Dust remover is a device that separates dust from flue gas. It is called dust collector or dust removal equipment. The performance of the dust collector is expressed by the amount of gas that can be treated, the resistance loss of the gas through the dust collector and the efficiency of the dust removal. At the same time, the price of dust collector, the cost of operation and maintenance, the length of service life and the difficulty of operation management are also important factors to consider its performance. Dust catcher is a common facility in boilers and industrial production.
purpose
The dust cover is set up in all the places where the ash is rised, and the dust gas is transported to the dust removal device through the pipeline gas path. After the gas solid separation is carried out, the dust is collected in the dust removal device, and the clean gas is introduced into the general pipe or a set of equipment directly discharged into the atmosphere, that is, the dust removal system, and the dust collector is in the system. The important part of the group. From the angle of ventilation and dust removal, dust is a small particle that can be found in the air for a long time. It is a dispersion system called aerosol, in which air is dispersed medium and solid particles are dispersed phase. A dust catcher is a device that separates this solid particle from the aerosol.
classification
According to the principle of action, duster can be divided into the following:
1. Dry type mechanical dust remover mainly refers to the dust removal equipment, such as settling chamber, inert dust collector, Cyclone Dust Collector and so on, which are designed with dust inertia action and gravity action. It is mainly used for the separation or concentration of high concentration coarse particle size dust.
2. Wet dust remover relies on water power to separate and capture dust particles, such as spray tower, scrubber, impact dust collector and Venturi Tube , etc., in the process of processing production, high concentration and large air volume of dust gases are used more. The separation efficiency of the thicker hydrophilic dust is higher than that of the dry type mechanical dust collector.
3, granular bed dust remover uses different particle size material accumulation layer as filter material to block the equipment for filtering the dust contained in the gas solution. It is mainly used for dust discharge points in the production process of building materials, metallurgy and so on. It often filters dust containing high concentration, coarse particles and high temperature.
4. The Bag Filter is a dedusting device that uses fiber fabric or filling layer as the filter medium. It has wide range of use, form, dust size and efficiency. It is mainly used in the place of collecting fine dust, that is, in the exhaust dust collection system and in the air inlet system. In recent years, because of the continuous development of new type of filter materials, the development of fiber filtering technology has also accelerated, new products continue to appear, and the application field is widening.
5. The Electrostatic Precipitator is a dust collector that introduces the dust air into the electrostatic field. Under the action of the high voltage electric field, the gas is ionized and produces electrons and positive ions. They move to the positive and negative poles respectively. When the dust particles flow through the working electric field, they are charged at a certain velocity to the opposite of their negative charge. The plates are removed and settled there, thus being removed from the airstream and collected in the electrostatic precipitator. The dust collector has the advantages of high dust removal efficiency, low resistance, and convenient maintenance and management. It has the same effect as bag filter in collecting fine dust particles.
New Dryer Bag Dust Collector,Dryer Bag Dust Collector,Dust Collector Of Dryer,Drying Machine Dust Collector
Botou Youjian Environmental Protection Equipment Co. LTD. , http://www.btdustmachine.com